Custom Designed Collaborative Robotic Assembly Cell Application
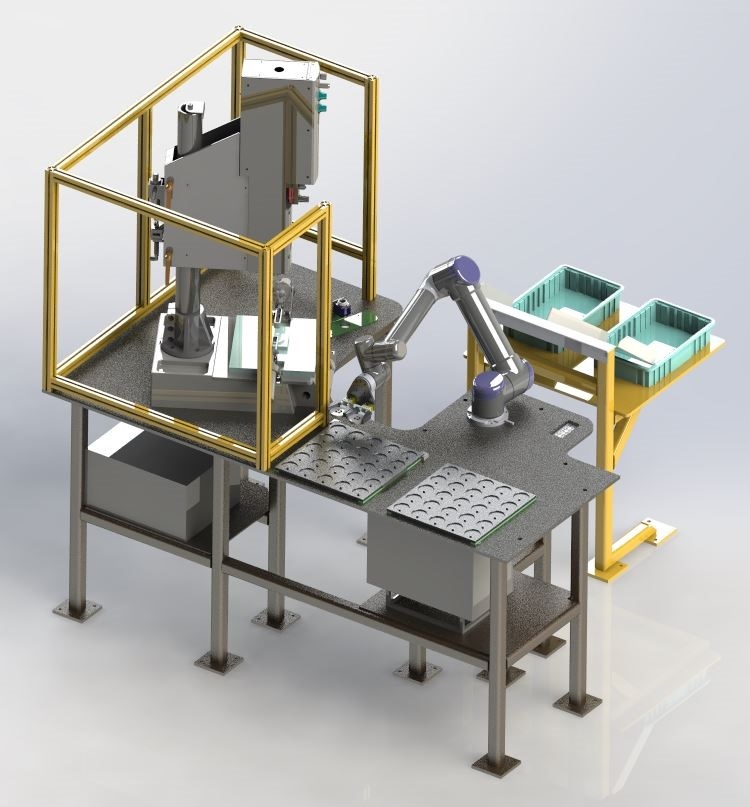
Upon completion of the risk evaluation it was determined that the guarding could be reduced substantially compared to a traditional robot. This allows the operators to interact with the robot cell while it is actively tending the welder.
The automated inspection is completed using a SICK smart camera to detect presence of cracks in the material caused by the weld process. Including the automated inspection task makes the automation of this tending application possible.
Project Description
This Custom Designed Robotic Cell is used for tending an ultrasonic welder.
Capabilities Applied/Processes
Cell Design
- Conception of Cell that Meets Unique Production Requirements
- Safety audit based on current RIA standards
- Create SolidWorks 3D Models of Cell Concept
Tooling Design
- End of Arm Tooling (EOAT) Design
- Automated vision inspection system
- Inspect each part after welding for stress cracks
- Isolate any potential defects
System Assembly
- Assemble program and pre-ship testing of the cell
Features/Benefits
Features
Utilizes Universal UR5 – Collaborative Robot
Use of a collaborative cell allows minimizing of physical guarding and associated safety control devices.
Automated tending of an ultrasonic welder by picking assemblies from a tray and placing them into the welder fixture. The fixture clamps the part and executes the weld cycle. When the weld cycle is complete the robot picks the assembly and presents it to the vision inspection station. Pass and Fail parts are isolated from each other.
Benefits
Provides production rates and consistency that is not capable with manual procedures.
Improved safety by removing the operator from the high noise area created by the ultrasonic welder.
More Info
Overall Cell Dimensions
72″ long x 60″ wide